If you’re reading this, then you already know that sublimation is an amazing technique that allows you to personalize your prints. However, poor sublimation transfer results sometimes occur. Sometimes we encounter banding, moisture issues, and even ghosting and outgassing.
If you've encountered any of these issues, we can help you solve them!
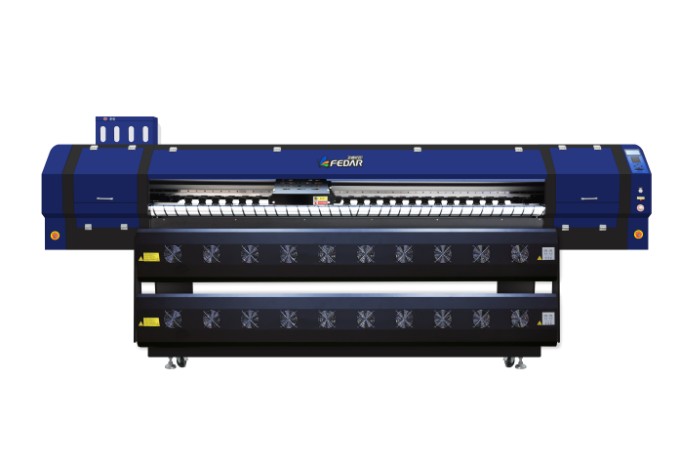
In this article, we will analyze each problem in the upper and lower phases, explain the cause of the problem, and give suggestions for solving it. Are you ready to overcome sublimation mistakes and create eye-catching, permanent designs? let's start!
1. Banding
Have you ever inspected a finished sublimation product and noticed strange horizontal or vertical lines on it? This is what we call “bundling” in biz.
Those unwanted lines or streaks that appear on your final sublimated product can be frustrating and, let’s be honest, they’re not pretty. But don’t worry – you can solve this issue with some simple troubleshooting.
Common causes of banding and how to solve themBanding is caused by a few simple issues. Clogged printer nozzles prevent ink from flowing freely, causing nasty lines on your prints. Additionally, low-quality sublimation paper or incorrect pressure settings on your heat press can also cause banding.
If you suspect a printer nozzle might be the culprit (which is common if you don't use your printer regularly), try cleaning it out. Most dye-sublimation printers have a self-cleaning feature, so if you have the option, give it a try first.
However, if you use an inkjet printer converter to use sublimation ink, the process is a little more in-depth. Start by running the cleaning program and test printing from a connected computer. This should fix the problem, but if the test page comes back streaky, it may have been contaminated by dust or dirt the last time you filled the ink tank. In this case, clean the ink cartridges, carefully fill them with new ink, and try again. If you still notice banding after this, you need to consider other potential causes, such as cheap sublimation paper and improper pressure settings on your heat press.
Buying cheap sublimation paper is tempting and may save you some upfront costs, but lower-quality paper can cause problems such as streaking on the production line because it also won't transfer the image. As for pressure settings, every heat press is different so it may take some trial and error to find the good position.
2.Moisture Issues
If you see spots or spots on your finished product, it may cause your design to not look as sharp and clean as you want.
Causes of moisture problems and how to solve themSo where do these annoying moisture problems come from? Typically, they are caused by residual moisture in the sublimation paper or the item being sublimated. If your sublimation paper or work area is in a humid environment like a garage or basement, moisture can sneak into your project.
A simple tip is to pre-press the sublimation paper for a few seconds before applying the design. This also helps to store the sublimation paper in a dry, cool place.
When it comes to managing humidity issues, the ultimate solution for a sublimation shop is to use a dehumidifier in the work area, especially if you work in a particularly humid climate.
We will answer the rest for you one by one in the next issue.
FEDAR dye sublimation digital printing machine has outstanding performance in the production of cycling clothing. It has an unparalleled advantage in terms of speed, which meets the needs of current fast fashion!
FEDAR sublimation printer company has absorbed and condensed a group of high-quality professional technicians and enterprising young management groups, formed a strong technical team and increasingly rigorous management system,providing customers with high-quality printing machines and services,and has established a good brand image and reputation in industry.