Making sublimated projects is a fun & creative way to express yourself and your interests, but sometimes, things may not be in your favor. Just like any other printing method, this all-over print process also has its fair share of problems; from overheating to ghosting, these issues can be pretty stressful.
If you're one of those who tackle these concerns often, don't be concerned. In this article, we'll discuss the 5 most common sublimation printing problems, what causes them, and, most importantly, how you can fix them for a worry-free printing experience.
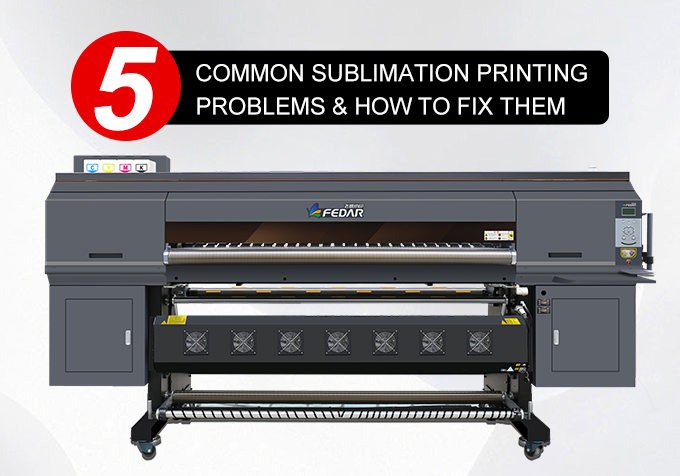
Problem 1: Ghosting
If we see a pattern of our transfer, like a shadow, a blurry image, or an outline, we're facing a normal issue known as ghosting. This problem generally occurs when the sublimation paper moves during the pressing process. But most likely when we open or close the heat press. Whatever we print, make two copies of it.
How to Fix It?
The moment is the key. Make sure that our print does not shift even an inch. The best way to do that is by using heat-resistant tape. Use enough thermal tape to hold the paper tightly onto the surface.
If we're working with fabrics, it's wise to use an adhesive spray to prevent any movement. Also, avoid using an auto-open press, as it can cause the paper to move if not taped down firmly.
Problem 2: Image Not Vibrant or Bright
If our printed design (no matter what we print) looks dull or less vibrant, this can be both: normal or an issue. In general, printed transfers may look insipid, but once they're pressed onto your sublimation blank, the colors will appear vibrant. However, if the colors still do not pop out after pressing, it may be a problem.
How to Fix It?
First, if we've just got our printer, filled the ink, and printed for the first time, it's normal for the colors to be dull. Just print a few more copies before trying again. If we've had the printer for a while, it could be due to incorrect time, temperature, or pressure settings.
Problem 3: Banding appears when printing a shirt
When we print on a shirt (or other clothing), we find that there is obvious banding, which makes the pattern on the clothes uneven. How to solve this problem?
How to Fix It?
We need to clean the print head and make sure there is no dry ink or any dirt on the print head. At the same time, we also need to align the print head and check whether the ink level is sufficient. If the ink is insufficient, it will also cause banding problems.
Take the printed long skirt as an example:
Problem 4: The printed color is too dark
At this time, Photoshop is the most important. (PS for short, it is image processing software) If we use the default settings of Photoshop, it will print darker colors and the effect of transferring to the printed skirt will be unsightly.
How to Fix It?
We need to adjust the printer settings and use PS to increase the brightness of the image.
Problem 5: Ink bleeding at the edge of the printed image
How to Fix It?
This is an easy fix, the simplest step is to adjust the heat press settings to reduce the heat press temperature by 10 degrees or less and then print a second time. Incidentally, we may also need to reduce the amount of ink used in the design in the meantime.
5 Common Sublimation Printing Problems & How to Fix Them?
It is not terrible to have problems with sublimation printing. What is important is that we need to know how to fix them. The above are 5 common sublimation problems and solutions. I hope that after reading this, it will be helpful for everyone to make their printed products more durable.
If there's anything we can do to further showcase machines' features, please let us know.
Email: sale@fedar.net
Whatsapp: +86 15515715397
Our company has over 30 models of printers with independent intellectual property rights and patents. Marketed under the esteemed brands of
Skycolor,
Stormjet, and
Fedar brands, these printers cover a wide range, including digital textile printers, UV printers, eco-solvent printers and more. Known for their exceptional quality and performance.